The working principle and technical characteristics and advantages of coke dry quenching technology
2024-05-09 17:00:51
The working principle and technical characteristics and advantages of coke dry quenching technology
Working principle of coke dry quenching technology: Coke dry quenching uses cold inert gas (150℃) to exchange heat with red hot coke (950~1050℃) in the dry quenching tank to cool the coke (200℃) and absorb the heat of the coke. The gas transfers heat to the dry coke quenching boiler to produce steam. The cooled inert gas is blown into the dry quenching tank by the circulating fan for recycling. The steam produced by the CDQ boiler is used to generate electricity.
Characteristics of dry coke quenching technology Compared with conventional wet coke quenching, dry coke quenching mainly has the following four advantages:
(1) Recover the sensible heat of red coke. The sensible heat of red coke accounts for 35% to 40% of the energy consumption of the coke oven, and dry coke quenching can recover 80% of the sensible heat of red coke. On average, 3.9-4.0MPa can be recovered for every 1t of coke extinguished, and 0.45t-0.55t of steam at 450℃. According to Japan's Nippon Steel's analysis of the effectiveness of energy-saving projects within its enterprise, including dry quenching coke, the results show that the energy saving of dry coke quenching equipment accounts for 50% of the total energy saving, indicating that dry coke quenching plays a decisive role in the energy-saving projects of steel companies.
(2) Improve coke quality. Compared with wet coke quenching, dry coke quenching avoids the adverse effects of rapid cooling of wet coke quenching on the coke structure, and its mechanical strength, wear resistance, and volume density are improved. The coke ratio increased by 3% to 6%, M10 decreased by 0.3% to 0.8%, and the reactivity index CRI decreased significantly. The improvement of metallurgical coke quality is extremely beneficial to reducing ironmaking costs, increasing pig iron production, and smoothing blast furnace operations, especially for large blast furnaces using coal injection technology. Large blast furnace smelting shows that the use of CDQ coke can reduce the coke ratio by 2.3% and increase the blast furnace production capacity by 1% to 1.5%. At the same time, while keeping the quality of the original coke unchanged, the use of dry coke quenching can expand the amount of weakly caking coal used in coking and reduce coking costs.
(3) Reduce environmental pollution. Conventional wet coke quenching, taking a coking plant with an annual output of 1 million tons of coke as an example, emits more than 600 tons of toxic gases such as phenol, cyanide, hydrogen sulfide, and ammonia, seriously polluting the atmosphere and surrounding environment. Coke dry quenching uses inert gas to cool the red coke in a closed dry quenching tank and is equipped with good and effective dust removal facilities, which basically does not pollute the environment. In addition, the production steam produced by dry coke quenching can avoid atmospheric pollution from boiler flue gases that produce the same amount of steam, reduce SO2 and CO emissions, and has good social benefits.
(4) Save water resources. The wet quenching process produces approximately 0.581t of steam containing phenol, cyanide, sulfide and dust for every 1t of red coke quenched. The corresponding dry quenching device can save 0.58t of water for every 1t of coke dry quenched.
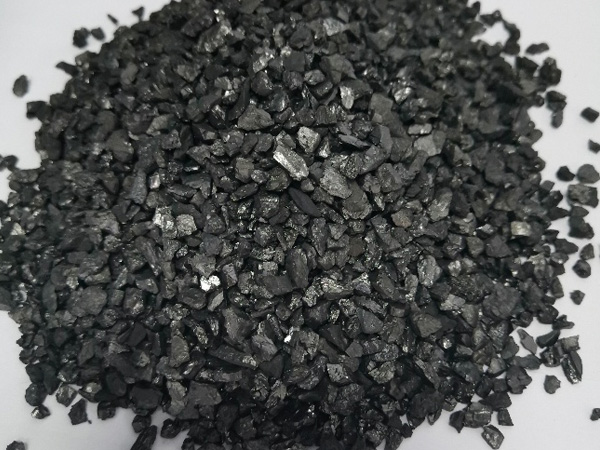
Calcined anthracite coal is anthracite that has been heat-treated and raw comes from the hi...
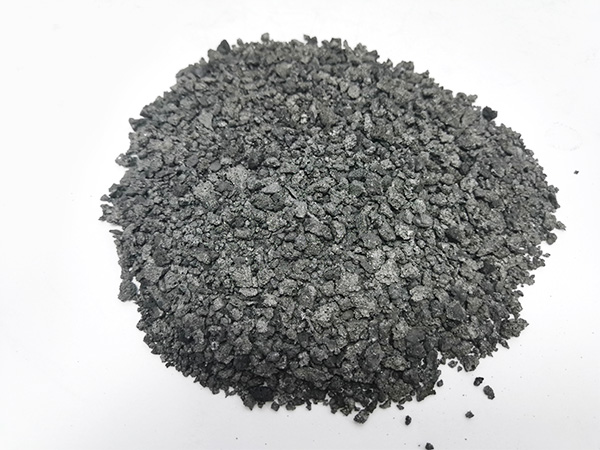
Coke Dry Quenching is an alternative to the traditional wet quenching of the coke. Coke is ...
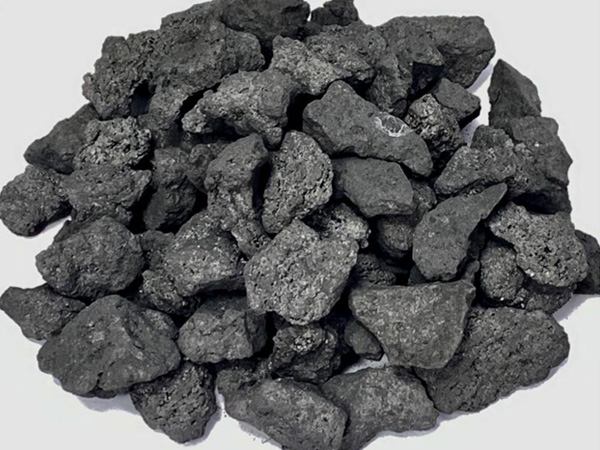
Coke Breeze is the by-product which is produced from the process of coke fragment, transpor...
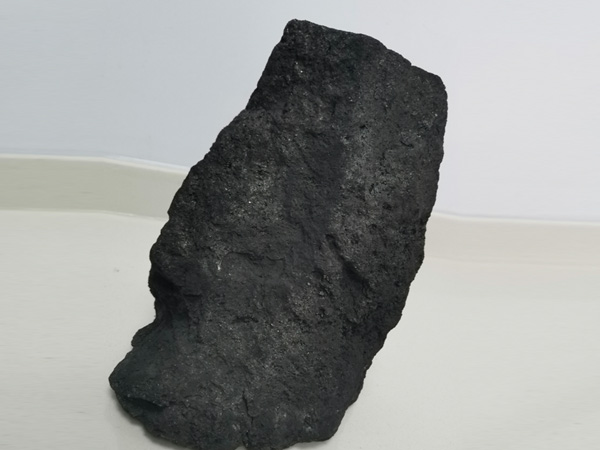
Metallurgical Coke plays an important role in melting furnace charge and overheat the molte...