The main factors affecting the absorption rate of the Carbon Raiser
2024-05-17 11:21:57
The main factors affecting the absorption rate of the Carbon Raiser
1 The influence of the particle size of the Carbon Raiser
The recarburization process using the Carbon Raiser includes the dissolution diffusion process and the oxidation loss process.The dissolution diffusion rate and the oxidation loss rate are different for different particle sizes of the Carbon Raiser.The absorption rate of the Carbon Raiser depends on the combined effect of the dissolution diffusion rate and the oxidation loss rate of the Carbon Raiser:in general,the Carbon Raiser particles are small,the dissolution rate is fast,and the loss rate is large;the Carbon Raiser particles are large,the dissolution rate is slow,and the loss rate is small.The selection of the particle size of the Carbon Raiser is related to the diameter and capacity of the furnace.In general,the larger the diameter and capacity of the furnace,the larger the particle size of the Carbon Raiser;conversely,the smaller the particle size of the Carbon Raiser.For electric furnace melting below 1t,the particle size of crystal graphite is required to be 0.5~2.5mm;the particle size of crystal graphite melting in 1t~3t electric furnace melting is required to be 2.5~5mm;the particle size of crystal graphite melting in 3t~10t electric furnace melting is required to be 5.0~20mm;the particle size of crystal graphite covered in the ladle is required to be 0.5~1mm.
2 Effect of the amount of Carbon Raiser added
Under certain temperature and chemical composition conditions,the saturation concentration of carbon in the molten iron is certain.The solubility limit of carbon in cast iron is([C%]=1.3+0.0257T-0.31[Si%]-0.33[P%]-0.45[S%]+0.028[Mn%](T is the temperature of the molten iron).At a certain saturation,the more Carbon Raiser is added,the longer the time required for dissolution and diffusion,the greater the corresponding loss,and the lower the absorption rate.
Tar Carbon Raiser
3 Effect of temperature on the absorption rate of Carbon Raiser
From the perspective of kinetics and thermodynamics,the oxidizability of molten iron is related to the equilibrium temperature of the C-Si-O system.That is,O in the molten iron will react with C and Si.The equilibrium temperature varies with the target C and Si content.When the molten iron is above the equilibrium temperature,carbon oxidation occurs first,and C and O generate CO and CO2.In this way,the carbon oxidation loss in the molten iron increases.Therefore,above the equilibrium temperature,the Carbon Raiser absorption rate decreases;when the recarburization temperature is below the equilibrium temperature,due to the lower temperature,the saturated solubility of carbon decreases,and the dissolution and diffusion rate of carbon decreases,so the yield is also lower;when the recarburization temperature is at the equilibrium temperature,the Carbon Raiser absorption rate is the highest.
4 Effect of stirring of molten iron on the absorption rate of Carbon Raiser
Stirring is conducive to the dissolution and diffusion of carbon,and prevents the Carbon Raiser from floating on the surface of molten iron and being burned.Before the Carbon Raiser is completely dissolved,the longer the stirring time,the higher the absorption rate.Stirring can also reduce the Carbon Raiser insulation time,shorten the production cycle,and avoid the burning of alloy elements in the molten iron.However,if the stirring time is too long,it will not only have a great impact on the service life of the furnace,but also after the Carbon Raiser is dissolved,stirring will aggravate the loss of carbon in the molten iron.Therefore,the appropriate stirring time of molten iron should be appropriate to ensure that the Carbon Raiser is completely dissolved.
5 Iron Influence of liquid chemical composition on the absorption rate of Carbon Raiser
When the initial carbon content in the molten iron is high,under a certain solubility limit,the absorption speed of the Carbon Raiser is slow,the absorption amount is small,the burn loss is relatively large,and the absorption rate of the Carbon Raiser is low.When the initial carbon content of the molten iron is low,the situation is the opposite.In addition,silicon and sulfur in the molten iron hinder the absorption of carbon and reduce the absorption rate of the Carbon Raiser;while manganese helps the absorption of carbon and increases the absorption rate of the Carbon Raiser.In terms of the degree of influence,silicon has the greatest influence,followed by manganese,and carbon and sulfur have less influence.Therefore,in the actual production process,manganese should be added first,then carbon,and finally silicon.
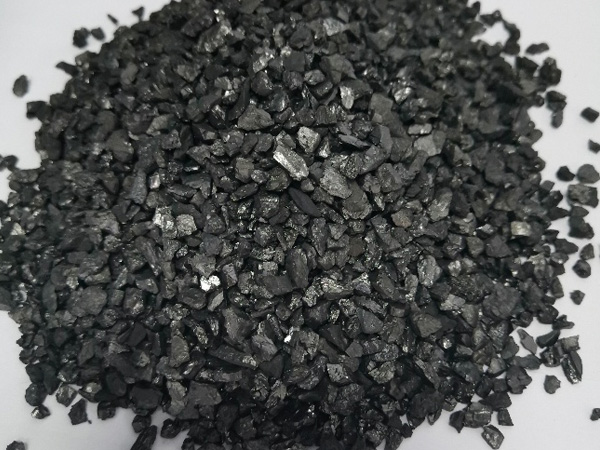
Calcined anthracite coal is anthracite that has been heat-treated and raw comes from the hi...
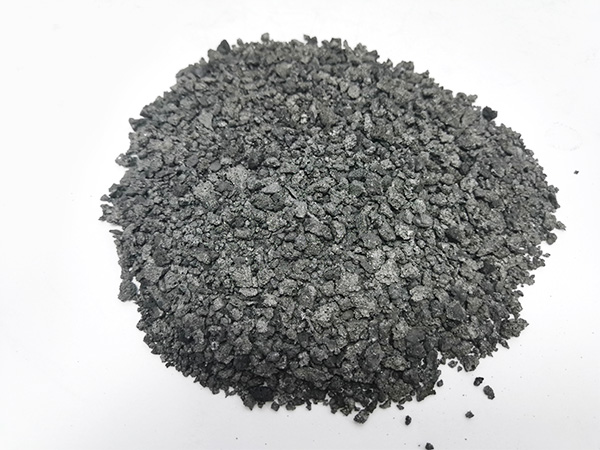
Coke Dry Quenching is an alternative to the traditional wet quenching of the coke. Coke is ...
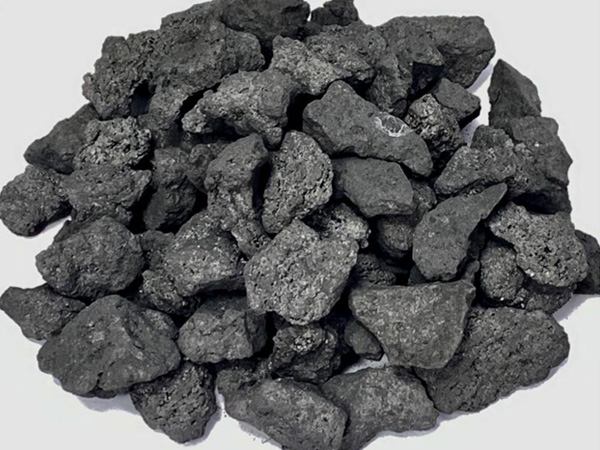
Coke Breeze is the by-product which is produced from the process of coke fragment, transpor...
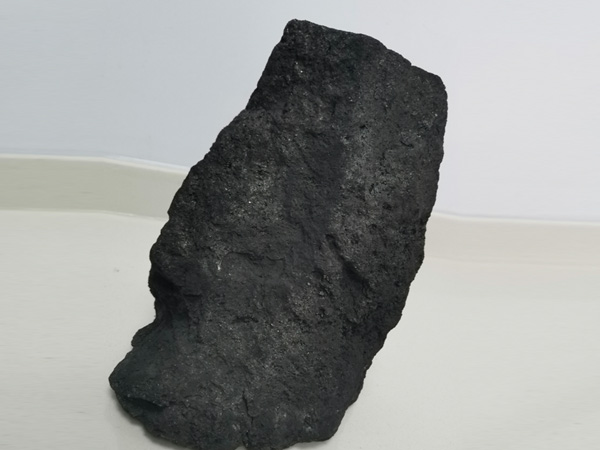
Metallurgical Coke plays an important role in melting furnace charge and overheat the molte...